Forse verlaging cyclustijd bij Brabant Alucast met boren van Mapal
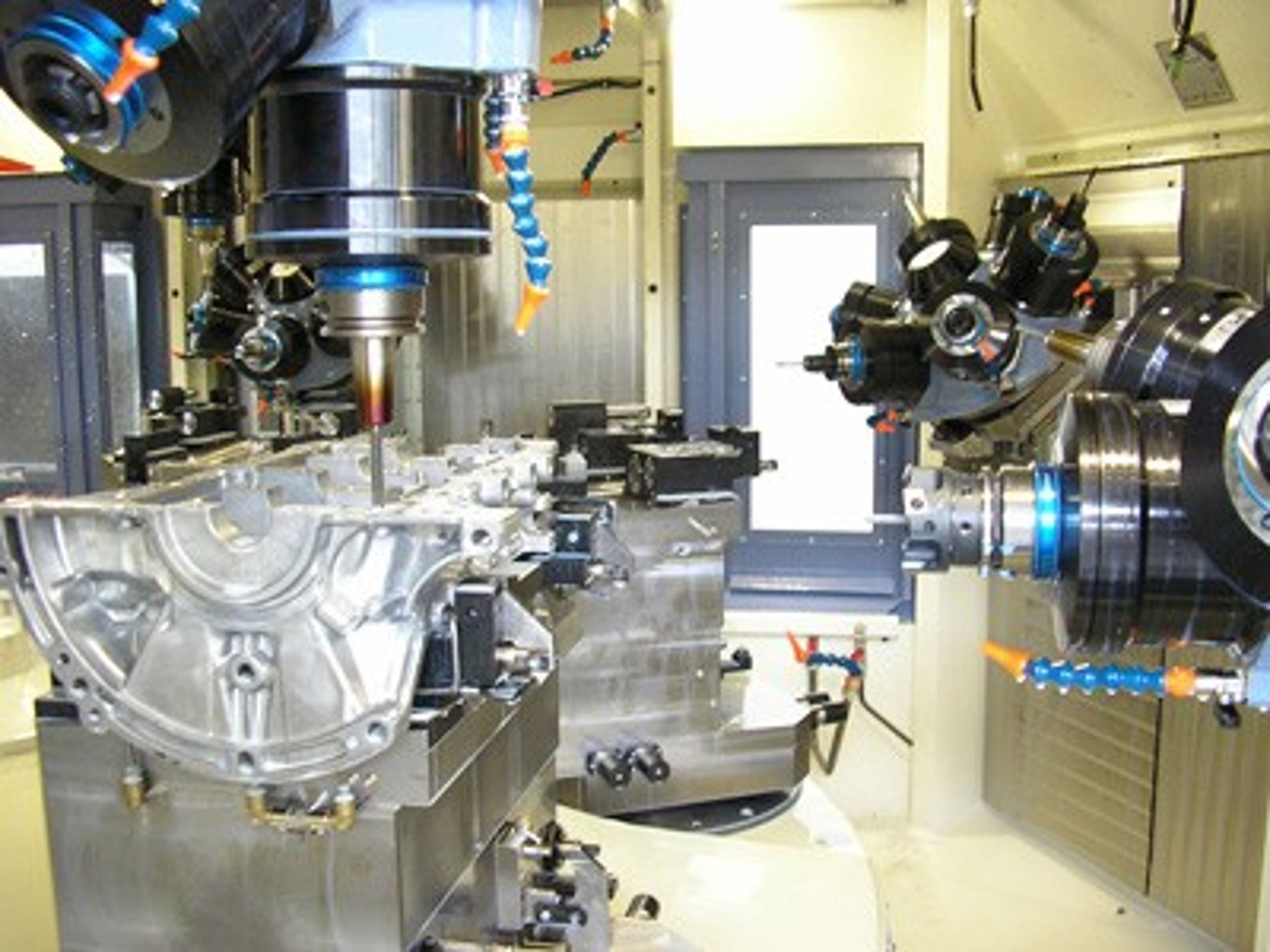
Boren onder moeilijke condities
Dankzij een boor van Mapal heeft Brabant Alucast bij de bewerking van carters het aantal boormeters verhoogd van 560 meter naar 12.288 meter. Ook de cyclustijd is fors omlaag gebracht. Gekozen is voor een gemodificeerde Mapal Tritan-Drill. De kenmerken van deze boor zijn een aangepaste coating, een optimalisatie van koelmiddeldoorvoer en het boren geschiedt met drie snijkanten.
Is het boren van 10 gaten met een diameter 10 mm en een diepte van een 80 mm in gietaluminium met een zo hoog mogelijke voeding zonder speciale eisen aan de tolerantie en ruwheid eigenlijk moeilijk? ‘Geen probleem’ zal menig werkvoorbereider zeggen. Er zitten echter wat addertjes onder het gras. De medewerkers van Brabant Alucast hebben dat ervaren.
In 2006 begon men met het gieten en bewerken van het bodemdeel van een carter voor PSA Peugeot Citroen. De seriegrootte bedraagt hierbij circa 480.000 stuks per jaar. Per product spreken we dan van tien gaten met de genoemde afmetingen. Inzetten van boren met PKD-wisselplaten (polykristallijne diamant) zouden de klus eenvoudig moeten klaren. Maar gereedschapbreuk in de transferstraat leidde tot machinestilstand en afkeur.
"Gereedschapbreuk is altijd problematisch omdat je nooit helemaal kunt voorkomen dat een foutief werkstuk bij de klant terechtkomt met reclamaties als gevolg", zegt Christiano Sala (parts & proces development engineer bij Brabant Alucast in Oss). "Bovendien kun je met een onvoorziene machinestilstand bij zo'n vergaand geautomatiseerde installatie niet zo eenvoudig om gaan als bij een bewerkingscentrum. Productieonderbrekingen zijn veel ingrijpender."
Niet alleen het thema gereedschapbreuk hield Brabant Alucast bezig. Ook de standtijd van 560 mm (7.000 gaten) die behaald werd met de PKD-boren en de cyclustijd bepaald, waren niet naar tevredenheid. Hoewel de automotivetoeleverancier de bewerking al had gesplitst in twee stations (zes en vier gaten) van de rotatietransfermachine, lukte het niet om de cyclustijd te reduceren tot minder dan de gewenste 45 s. "Een groot aantal factoren bemoeilijkten de bewerking", zegt Sala terugkijkend.
Lastig Het gat is aan beide zijden van het werkstuk voorgegoten in de vorm van een blind gat. Dit is noodzakelijk omdat de gaten zich bevinden in het gedeelte van de lagering van de motor, waar een hoge hardheid en minimale porositeit vereist zijn. Na ongeveer een jaar schakelde Brabant Alucast over van een PKD-boor op een hardmetalen standaardboor met twee spaangroeven. Maar dit maakte voor de gereedschapbreuk en standtijd weinig uit.
Na een onverwacht hoge vraag in 2010, die tot een leveringstekort leidde, veranderde Brabant Alucast van boorleverancier. De nieuwe leverancier beschikte over een gereedschapslijperij in de buurt en zette een hardmetalen boor met twee spaangroeven in de bewerkingsmachine. Na een paar maanden werd besloten om een boor met drie groeven te gebruiken, maar ook dit gaf niet voldoende verbetering.
Sala: "De beslissende doorbraak kwam in 2012.
Mapal zette de kentering in gang met een hardmetalen boor met twee spaangroeven die was aangepast aan de specifieke eisen van de bewerking. Deze gecoate boren hebben een speciale snijkantgeometrie en extra koelkanalen halverwege de spiraalgroef. Er is een goed resultaat geboekt: De standtijd nam toe tot 7.600 m (100.000 gaten) bij een voeding van 0,5 mm/omw. In vergelijking met de PKD-boren werd de levensduur verhoogd met een factor dertien. Dankzij die verhoging hoeft Brabant Alucast de boor niet langer te herslijpen. Sala: "We hebben duidelijk onze doelen bereikt in termen van procesbetrouwbaarheid".
Agressief In een volgende optimalisatiestap besloot Norbert Thoma, technisch adviseur bij Mapal, om gebruik te maken van een aangepaste hardmetalen Tritan-Drill.
Deze boor wordt onder andere gekenmerkt door een 'agressieve', zelfcentrerende dwarssnijkant die zich in het materiaal vastbijt bij het eerste contact met het werkstuk en de boor in positie houdt zodat deze niet uit het centrum wegloopt.Mapal ontwikkelde deze boor begin 2014 met het behoud van de snijkantgeometrie, coating en koelkanalen van de voorheen gebruikte boren met twee spaangroeven. Een Tritan-Drill op deze wijze uitgevoerd, met drie snijkanten, vergroot de boorprestatie verder tot 12.288 m (153.600 gaten).
Verder werd de voeding verhoogd tot 0,74 mm bij een toerental van 4.200 min1.
De totale bewerkingstijd is gereduceerd tot 37 s.
Vergeleken met de PKD boren correspondeert dit met een reductie van de bewerkingstijd met ruim 18%. "Het resultaat van de intensieve samenwerking met Mapal heeft ons allemaal opnieuw overtuigd", vat Christiano Sala samen. "Doordat er geen onderbrekingen meer zijn loopt de machine langer door, maar bewerkt ook meer onderdelen in minder tijd".
Boren lastig
Omdat er bij het gieten van aluminium afwijkingen in de positie van de voorgevormde gaten kunnen optreden, heeft de boor de neiging om weg te lopen.
De resulterende kracht op de boor leidt dan bijna altijd tot gereedschapbreuk.
Verder is het koelen en smeren van de koelkanalen aan de kopse kant niet langer gegarandeerd wanneer de boor de bodem van het tegenoverliggende blinde gat binnentreedt en de koel- of smeerdruk plotseling wegzakt. Bovendien mogen zich geen bramen vormen wanneer de boor uit het werkstuk treedt, omdat vanwege de tijd en kosten alleen vanaf één zijde geboord wordt en repareren geen optie is. Dit maakt het boren van de carters lastig.
Bron:Artikel Metaal Magazine jaargang 53 10-2015